POM - Polyoxymethylene
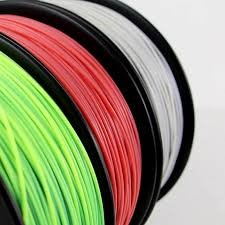
Polyoxymethylene (POM), also known as polyacetal or acetal, was discovered by the German chemist Herman Staudinger. After his discovery the polymer was not commercialized due to problems with thermal stability.
Around 1960 DuPont commercialized POM production under the brand name Delrin. A few years later, US company Celanese started also sales of their POM named Celcon. A year later the German chemical company Hoechst also started polyacetal production of the brand name Hostaform.
Later on the company Celanese was introduced; a joint venture between Celanese and Hoechst, creating the world’s largest acetal producer. Celanese (part of the Celanese company) is still the biggest POM producer in the world, which just opened a new POM plant on Hoechst Industrial Park, close to Frankfurt.
Nowadays there are more players in the POM world. Besides Celanese with Hostaform and Celcon the biggest are; DuPont with Delrin, Polyplastic with Duracon, BASF with Ultraform, Kolon Plastics with Kocetal, Zaklady with Tarnoform, Yuntianhua with Yuntianhua POM and BlueStar with BlueStar POM.
In the polyacetal business a lot more POM brands are visible in the market, compounders, distributor and traders have created their own brands like Resinex POM.
Polyoxymethylene can be divided into two groups:
- Homopolymer POM;
- Copolymer POM.
Starting from methanol, formaldehyde is created and POM homopolymer is created (e.g. Delrin) if this is directly polymerized. For POM copolymer, formaldehyde is converted to trioxane and this is polymerized, together with a co-monomer, to a POM copolymer (e.g. Hostaform).
The POM homopolymer has a higher crystallinity compared with the POM copolymer, on the other hand chemical resistance of the copolymer is higher. This results in a higher stiffness for the homopolymer and less thermal degradation of the POM copolymer during production and in the field.
POM offers many excellent properties including:
- High stiffness;
- Low wear;
- Good resilience;
- Low water absorption.
The most common forming processes for polyacetal are injection moulding and extrusion (sheets and rods), but also blow moulding and rotational moulding are is possible.
POM is mainly used for technical parts where the mentioned mechanical properties are giving it an advantage over other plastics.
Typical polyoxymethylene applications are:
- Gears;
- Springs;
- Chains;
- Screws;
- Handles;
- Zippers;
- Clips;
- Fuel pumps;
- Inhalers;
- Furniture sliders.
Around 1960 DuPont commercialized POM production under the brand name Delrin. A few years later, US company Celanese started also sales of their POM named Celcon. A year later the German chemical company Hoechst also started polyacetal production of the brand name Hostaform.
Later on the company Celanese was introduced; a joint venture between Celanese and Hoechst, creating the world’s largest acetal producer. Celanese (part of the Celanese company) is still the biggest POM producer in the world, which just opened a new POM plant on Hoechst Industrial Park, close to Frankfurt.
Nowadays there are more players in the POM world. Besides Celanese with Hostaform and Celcon the biggest are; DuPont with Delrin, Polyplastic with Duracon, BASF with Ultraform, Kolon Plastics with Kocetal, Zaklady with Tarnoform, Yuntianhua with Yuntianhua POM and BlueStar with BlueStar POM.
In the polyacetal business a lot more POM brands are visible in the market, compounders, distributor and traders have created their own brands like Resinex POM.
Polyoxymethylene can be divided into two groups:
- Homopolymer POM;
- Copolymer POM.
Starting from methanol, formaldehyde is created and POM homopolymer is created (e.g. Delrin) if this is directly polymerized. For POM copolymer, formaldehyde is converted to trioxane and this is polymerized, together with a co-monomer, to a POM copolymer (e.g. Hostaform).
The POM homopolymer has a higher crystallinity compared with the POM copolymer, on the other hand chemical resistance of the copolymer is higher. This results in a higher stiffness for the homopolymer and less thermal degradation of the POM copolymer during production and in the field.
POM offers many excellent properties including:
- High stiffness;
- Low wear;
- Good resilience;
- Low water absorption.
The most common forming processes for polyacetal are injection moulding and extrusion (sheets and rods), but also blow moulding and rotational moulding are is possible.
POM is mainly used for technical parts where the mentioned mechanical properties are giving it an advantage over other plastics.
Typical polyoxymethylene applications are:
- Gears;
- Springs;
- Chains;
- Screws;
- Handles;
- Zippers;
- Clips;
- Fuel pumps;
- Inhalers;
- Furniture sliders.