PC - Polycarbonate
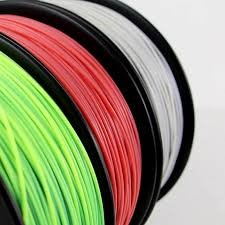
Polycarbonate (PC) has a unique combination of toughness, optical transparency, rigidity and strength. PC also displays excellent electrical properties. Polycarbonate is amorphous and transparent.
Polycarbonate resins are produced mainly via a polycondensation reaction, pioneered by Bayer Material Science and GE Plastics (today Sabic Innovative Plastics), involving the reaction of BPA (bis- phenol A) with phosgene (COCl2). Polycarbonate (PC) melt-phase processes were developed in the 1990s.
Polycarbonate is inherently one of the most transparent polymers. At the same time PC can be compounded into different colors, from transparent tints to opaque solid colours. Polycarbonate aesthetics are at the highest level within the range of engineering polymers.
The molecular chain weight of PC can be designed during polymerization to give the polycarbonate many different Melf Flow Rates (MFR or MFI). The Melt Flow Rate of PC typically ranges from 3 to 80 g/10 min. Polycarbonate is suitable for both injection moulding and extrusion moulding. Polycarbonate is also suitable for extrusion blow moulding.
Polycarbonate can be produced with many different product features including : new environmentally conforming flame retardant technology, scratch resistance, toughness, heat resistance, weatherability, biocompatibility, optical quality, and compliance with stringent FDA and USP requirements.
Polycarbonate has superior UV stability and this can be even further improved by adding UV stabilizers. Other additives can be heat boosters or additives improving ESCR (environmental stress cracking). PC can be filled with glass fiber to increase further the rigidity.
Typical applications of polycarbonate include:
- Automotive: Headlights, safety windows
- Sheet + profile: Roofing & windows, vandal proof applications
- Electrical: plugs, sockets, meters, security, safety
- Household appliances: blender bowls, microwave doors
- Consumer goods and housewares: chocolate moulds
- Safety devices: goggles, helmets
- Medical: dialyzer housings
- Lighting: globes, diffusers, traffic lights
- Compact discs: CD-ROM, CD-recordable, DVD
Polycarbonate resins are produced mainly via a polycondensation reaction, pioneered by Bayer Material Science and GE Plastics (today Sabic Innovative Plastics), involving the reaction of BPA (bis- phenol A) with phosgene (COCl2). Polycarbonate (PC) melt-phase processes were developed in the 1990s.
Polycarbonate is inherently one of the most transparent polymers. At the same time PC can be compounded into different colors, from transparent tints to opaque solid colours. Polycarbonate aesthetics are at the highest level within the range of engineering polymers.
The molecular chain weight of PC can be designed during polymerization to give the polycarbonate many different Melf Flow Rates (MFR or MFI). The Melt Flow Rate of PC typically ranges from 3 to 80 g/10 min. Polycarbonate is suitable for both injection moulding and extrusion moulding. Polycarbonate is also suitable for extrusion blow moulding.
Polycarbonate can be produced with many different product features including : new environmentally conforming flame retardant technology, scratch resistance, toughness, heat resistance, weatherability, biocompatibility, optical quality, and compliance with stringent FDA and USP requirements.
Polycarbonate has superior UV stability and this can be even further improved by adding UV stabilizers. Other additives can be heat boosters or additives improving ESCR (environmental stress cracking). PC can be filled with glass fiber to increase further the rigidity.
Typical applications of polycarbonate include:
- Automotive: Headlights, safety windows
- Sheet + profile: Roofing & windows, vandal proof applications
- Electrical: plugs, sockets, meters, security, safety
- Household appliances: blender bowls, microwave doors
- Consumer goods and housewares: chocolate moulds
- Safety devices: goggles, helmets
- Medical: dialyzer housings
- Lighting: globes, diffusers, traffic lights
- Compact discs: CD-ROM, CD-recordable, DVD